Gyratory screen is designed to provide precise and accurate sieving of material, it adopts eccentric mechanism which drives the material on the screen surface do uniform gyratory reciprocating swing motion,the materials are spread and stratified on the full screen surface, then the gyratory reciprocating motion gradually changes to an elliptical motion at the centre which is good for material sieving,a straight-line motion at the discharge end,the material movement track becomes short and then materials flow out of the outlet.Gyratory screener is widely used in chemical,fertilizer,metallurgical,ceramsite,refractory materials,grain, food, abrasives, mining and other industries in the sizing process of material accurate screening.
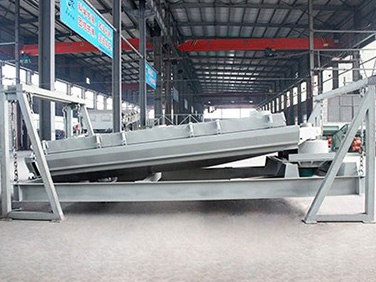
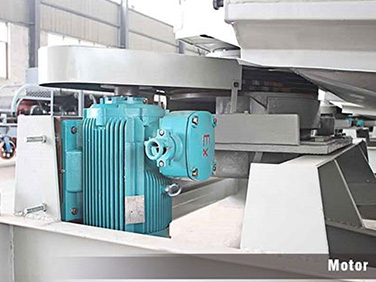
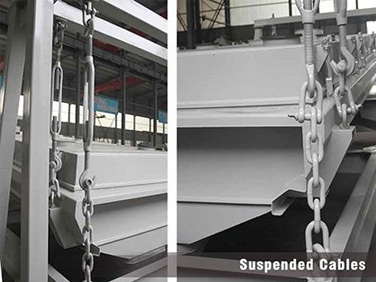